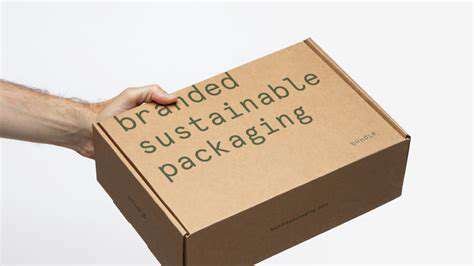
The Environmental Impact of Conventional Packaging
Carbon Emissions from Standard Packaging
Most commercial packaging today relies on materials such as cardboard, plastic polymers, and paper products, all of which leave a substantial environmental footprint. The creation of these materials typically begins with resource extraction, which frequently results in forest degradation, ecosystem disruption, and water contamination. Additionally, the energy required for manufacturing, transporting, and eventually discarding these items generates massive amounts of greenhouse gases that accelerate global warming. Many of these materials have extended lifespans when dumped in landfills, where they interfere with natural biodegradation and leach toxic compounds into the environment.
Assessing the full carbon impact of standard packaging requires examining its complete lifecycle from raw material sourcing to final disposal. This comprehensive understanding is vital for creating eco-friendly alternatives and refining current methods. Key strategies for reducing environmental harm include minimizing energy use during production, streamlining shipping logistics, and expanding recycling programs.
Waste Accumulation and Landfill Challenges
Perhaps the most urgent problem with conventional packaging is the staggering quantity of waste it produces. The enormous volumes of discarded packaging materials create severe environmental pressures. Landfills not only consume precious land but also emit methane - an extremely potent greenhouse gas - as organic matter decomposes. This breakdown process can also release dangerous chemicals into nearby soil and water systems, polluting natural habitats and creating health hazards.
Standard packaging disposal frequently leads to serious landfill complications. Since many of these materials don't biodegrade naturally, they remain in the environment indefinitely. This situation contributes to the critical issue of overfilled landfills and underscores the need for environmentally responsible waste management approaches.
Resource Consumption and Material Acquisition
The production of conventional packaging materials depends heavily on extracting natural resources, leading to significant depletion. The demand for wood pulp, plastic components, and other raw materials puts tremendous pressure on ecosystems, causing deforestation, wildlife habitat destruction, and depletion of essential minerals. Implementing sustainable sourcing practices is crucial for reducing the ecological impact of traditional packaging while preserving these resources for future generations.
Irresponsible material sourcing can have catastrophic effects on natural systems. Deforestation not only destroys animal habitats but also leads to soil erosion, water pollution, and loss of biodiversity. Extracting fossil fuels for plastic production worsens climate change while exhausting limited natural reserves. Transitioning to ethical sourcing methods and renewable materials is essential for addressing these concerns.
Effects on Wildlife and Natural Systems
The production and disposal of conventional packaging can severely damage biodiversity and ecosystem stability. Clearing forests for wood pulp, destroying habitats for raw materials, and pollution from waste sites all contribute to declining biodiversity. Disrupting natural ecosystems can trigger chain reactions throughout food webs and impair overall environmental health. Packaging decisions must carefully consider these broad ecological consequences.
Traditional packaging materials often lead to habitat loss and fragmentation, affecting numerous plant and animal species. Pollution from disposal sites, including landfills and incinerators, can taint water supplies and soil, upsetting natural ecological balances. Moreover, non-biodegradable materials can have lasting negative impacts on biodiversity by interfering with natural decomposition and potentially harming wildlife through ingestion or entanglement.
Contamination from Production and Disposal
Manufacturing processes for many standard packaging materials, especially plastics and paper products, generate substantial pollution. Airborne emissions, water contaminants, and hazardous byproducts from production can negatively affect both human health and the environment. Furthermore, disposing of conventional packaging often releases toxic substances into ecosystems, compounding pollution problems.
The environmental consequences of traditional packaging extend throughout manufacturing and disposal cycles. Plastic production pollution includes greenhouse gases from energy consumption, chemical releases during processing, and waste generation. Improper disposal methods can leach harmful compounds into soil and water, creating widespread risks for public health and the environment. Adopting sustainable packaging solutions is critical for reducing these pollution threats.
Breakthrough Eco-Friendly Packaging Solutions
Plant-Derived Plastics
Bioplastics represent a viable substitute for conventional petroleum-based plastics. Sourced from renewable materials like corn starch, sugarcane, and plant oils, these innovations offer a more sustainable packaging approach. While bioplastics demonstrate clear advantages regarding reduced carbon emissions compared to traditional plastics, current production methods and material characteristics often require refinement. Key areas for improvement include cost efficiency, material strength, and performance under various storage conditions, particularly for dry goods packaging needs.
A critical factor in bioplastic development involves establishing more reliable supply networks. Consistent and efficient raw material sourcing is essential for scaling production and competing economically with conventional plastics. Ongoing research focuses on enhancing the protective qualities of plant-based materials to effectively block moisture and oxygen - crucial factors for preserving dry goods quality during shipping and storage.
Biodegradable Packaging Alternatives
Compostable packaging materials provide a potential zero-waste solution that could dramatically reduce long-term waste accumulation. These plant-based materials are engineered to decompose into natural elements under proper composting conditions. However, effective breakdown requires specific environmental factors, and the limited availability of suitable composting facilities presents a major obstacle to widespread adoption.
The primary challenge with compostable packaging involves guaranteeing complete biodegradation across diverse disposal environments. Various dry goods have distinct packaging requirements, and materials must accommodate these needs without compromising compostability. For instance, packaging must endure handling and storage conditions while remaining compostable. Additionally, consumer participation in proper disposal is vital for success. Clear instructions must accompany packaging to ensure correct composting methods.
Preventing cross-contamination presents another important consideration. Compostable packaging must be designed to avoid transferring undesirable substances to packaged dry goods, maintaining product safety and quality. This is especially critical for dry goods sensitive to contamination or requiring strict hygiene standards.
Developing standardized composting procedures and clear labeling guidelines for compostable packaging is essential for broad acceptance. Both consumers and businesses need transparent information about proper disposal methods and environmental benefits.
Well-designed compostable packaging systems can substantially reduce waste while supporting circular economy principles. Successful implementation requires cooperation between manufacturers, consumers, and waste management providers.
Creating Reusable and Long-Lasting Packaging
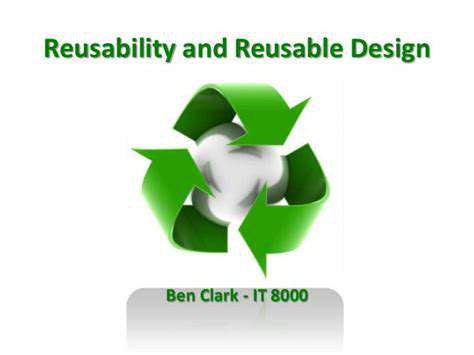
Designing for Extended Utility
A fundamental principle of successful design involves anticipating potential future modifications and evolving needs. Forward-looking design choices that emphasize adaptability and modular construction ensure products remain functional and relevant for extended periods. This proactive approach not only prolongs product lifecycles but also minimizes the need for expensive redesigns.
By accounting for possible future upgrades, expansions, or entirely new applications, designers create foundations supporting long-term viability. This requires understanding how products might be used and modified throughout their lifespan, then structuring them to accommodate these potential developments.
Modular Construction Methodology
Implementing modular design allows components to be easily replaced, updated, or repurposed. This reduces future maintenance and upgrade complexity. Modular approaches promote flexibility, streamlining modification processes over time.
Modular design divides systems into independent, interchangeable units. Each module can be developed and tested separately, reducing risks and enabling faster improvements. This also simplifies adding new features, as they can be implemented within specific modules without affecting entire systems.
Longevity and Structural Integrity
Durable designs prioritize withstanding prolonged use through careful material selection, construction methods, and stress point analysis. Focusing on durability extends product lifespans while enhancing value by reducing premature replacement needs.
Designers must thoroughly evaluate anticipated environmental conditions and potential stresses throughout a product's lifecycle. Robust materials and appropriate construction techniques ensure products endure expected usage while maintaining functionality. This approach minimizes failure risks and maximizes operational longevity.
Expandability and Flexibility
Scalable designs adapt to growing demands without major modifications. Well-designed systems should accommodate expanding user bases, increasing data volumes, or additional features without complete redesigns. Designing for scalability ensures products can manage future growth and evolving requirements.
User Interface and Serviceability
Intuitive, easy-to-use designs simplify maintenance and support. Clear documentation, straightforward interfaces, and well-defined procedures enhance product maintainability. Effective documentation can dramatically reduce troubleshooting and maintenance time. This contributes significantly to product success and longevity.
Well-designed interfaces and intuitive controls decrease error likelihood, making products easier to operate and maintain. This simplifies future adjustments or repairs, reducing costs and downtime while improving user experience and reinforcing long-term value.
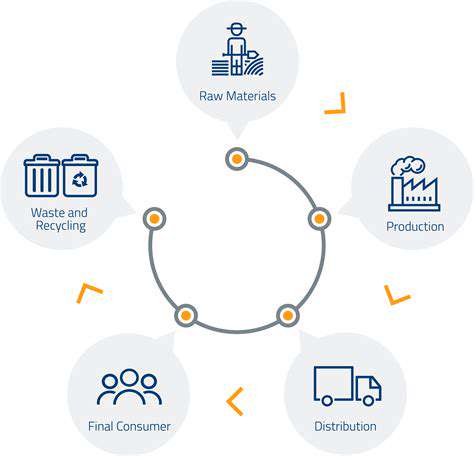